What is Rubber Vacuum Injection Molding Vulcanization?
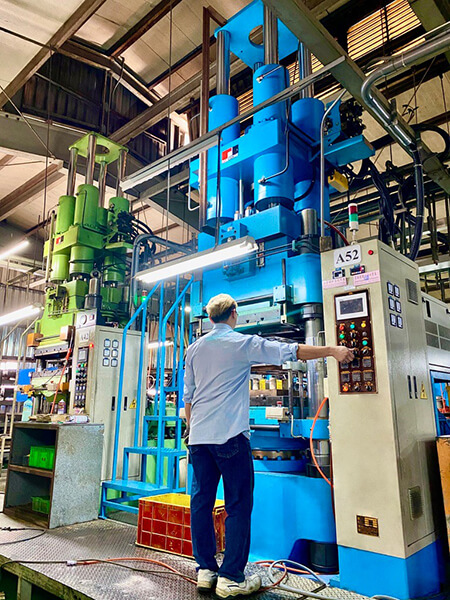
What is vacuum injection vulcanization molding technology?
Rubber vacuum injection vulcanization molding technology combines the principles of injection molding and vacuum technology, with an added vulcanization process, to produce high-quality rubber parts. The core of this technology lies in utilizing a vacuum environment during the injection molding process to eliminate defects caused by air, thereby improving the density and uniformity of the final product. Here is an explanation of the main steps and features of this technology:
1. Material Preparation
Select the appropriate uncured rubber compound, formulated and blended according to the requirements of the final product. These rubber mixtures typically include rubber base material, fillers, vulcanizing agents, and other necessary additives.
2. Vacuuming
Before injection molding, the mold is vacuumed to eliminate air within the mold. This step is crucial as it significantly reduces or eliminates bubbles and voids that can occur in the rubber molding process, which would affect the quality and performance of the product.
3. Injection Molding
Heat the prepared uncured rubber mixture to a flowable state, then quickly inject it into the mold cavity under a vacuum environment using an injection machine. As the rubber material fills the mold, the vacuum state helps to eliminate air from the material, ensuring that the rubber densely fits into every cavity of the mold.
4. Demolding
After vulcanization is complete, the finished product is removed.
Technical Advantages
- High-quality Products: Injection in a vacuum environment helps reduce or eliminate bubbles and defects in the product, improving product quality.
- Increased Production Efficiency: The injection molding process is highly automated, allowing for rapid production, particularly suitable for mass production.
- High Material Utilization: The injection molding process allows for precise control of the amount of rubber material used, reducing waste.
- Suitable for Complex Shapes: Injection molding is suitable for producing parts with complex shapes, and vacuum assistance can further improve the quality of complex parts.
Rubber vacuum injection vulcanization molding technology provides an effective method for producing high-quality rubber parts, especially suitable for applications requiring high quality and precision. However, the application of this technology requires consideration of its higher equipment and operational costs, as well as the technical and operator requirements. Zong Yih Rubber possesses both compression molding and injection molding expertise, evaluating the best production technology for customers at the lowest cost to ensure product quality. Contact us today to learn more about our rubber injection molding capabilities and how we can meet your specific needs.