What is Rubber Vacuum Compression Molding Vulcanization?
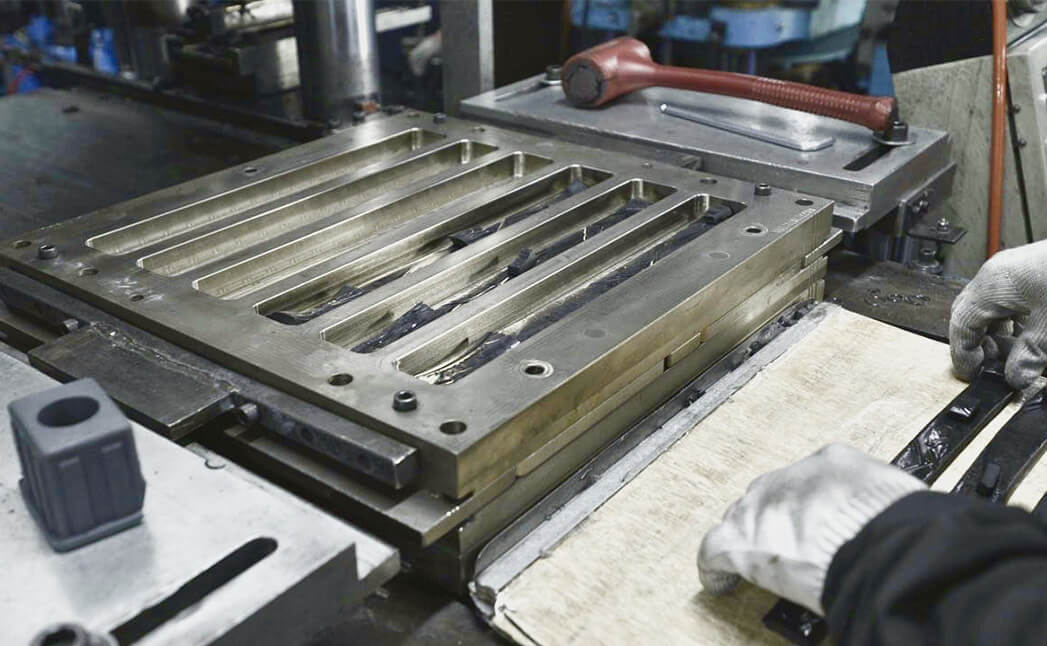
What is rubber vacuum compression molding vulcanization technology?
Rubber vacuum compression molding vulcanization technology is a rubber product production method that combines vacuum forming and vulcanization processes. This technique is primarily used to produce precise, high-quality rubber parts, particularly suitable for applications that require minimal bubbles and defects. The process of rubber vacuum compression molding vulcanization not only involves shaping the rubber material into a specific mold shape but also includes vulcanizing in a bubble-free environment, thereby enhancing the overall quality and performance of the molded product. Here are the main steps and features of this technology:
- Material Preparation: Select the appropriate uncured rubber compound, formulated and blended according to the requirements of the final product. These rubber mixtures typically include rubber base material, fillers, vulcanizing agents, and other necessary additives.
- Preheating and Preforming: Heat the rubber mixture to an appropriate temperature to make it soft and pliable for molding, but not yet starting the vulcanization process.
- Mold Design and Preparation: Design and manufacture precision molds, where the shape and details of the mold determine the appearance and dimensions of the final product. The mold must be able to withstand the high temperatures and pressures of the molding process.
- Vacuum Compression Molding: Place the preheated rubber in the mold, start the vacuum system to remove air from inside the mold, creating a vacuum state. The vacuum environment in this step helps to eliminate defects and inconsistencies caused by air, ensuring the density and uniformity of the molded product.
- Vulcanization Process: Vulcanize the rubber by heating the mold under vacuum conditions. Vulcanization is a key step in rubber product manufacturing, which improves the physical properties of rubber, such as elasticity, abrasion resistance, and temperature resistance, by adding sulfur or other vulcanizing agents.
- Demolding: After vulcanization, remove the molded rubber part from the mold.
The application of this technology brings several advantages but also has some disadvantages. Here are four advantages:
Advantages
- Enhances product quality: The vacuum process effectively reduces defects and imperfections caused by air in the product.
- More economical: Reduces waste and saves costs.
- Diversity and flexibility: Suitable for various complex and intricate product designs.
Zong Yih Rubber's Commitment
Rubber vacuum compression molding vulcanization technology provides a solution for producing high-quality rubber parts, particularly suitable for applications with high demands on quality and performance. However, the application of this technology requires consideration of its relatively high costs and technical requirements. At Zong Yih Rubber, we commit to utilizing this innovative technology to offer our customers higher quality, more diverse rubber products. Through continuous technological innovation and commitment to quality, we look forward to growing with our customers and creating more possibilities. In conclusion, if you're looking for high-quality rubber parts produced by a reliable and experienced manufacturer, look no further than Zong Yih Rubber Industrial. Contact us today to learn more about our compression molding capabilities and how we can meet your specific needs.